10,000 sq. ft.
Hartland, Vermont
APG New England, an Oldcastle® company
Cranston, Rhode Island
Gill Engineering
SRG Engineering
Cold River Bridges LLC
Walpole, New Hampshire
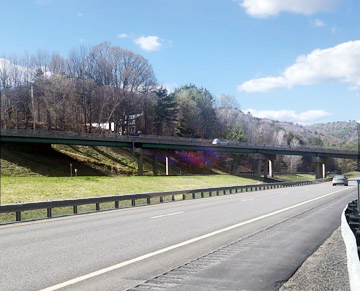
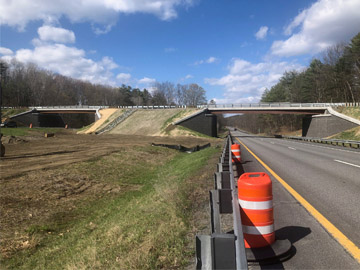
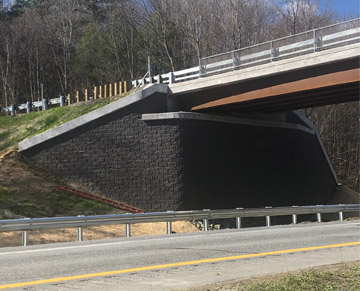
10,000 sq. ft.
Hartland, Vermont
APG New England, an Oldcastle® company
Cranston, Rhode Island
Gill Engineering
SRG Engineering
Cold River Bridges LLC
Walpole, New Hampshire
Deterioration of the superstructure of TH 41 Bridge 37D in Hartland, Vermont, posed a risk to heavily trafficked Interstate 91, running below the bridge. State of Vermont Agency of Transportation (VTrans) inspectors warned of the potential for full-depth pop-outs and risks of concrete falling onto the interstate below. Additionally, the bridge was not wide enough for the state’s snowplows. An initial engineering study recommended replacing the superstructure, meaning everything above the piers.
Rather than replace the superstructure of the existing bridge, VTrans found it more economical to replace the entire bridge using the innovative Geosynthetic Reinforced Soil-Integrated Bridge System (GRS-IBS) along with the Diamond Pro® Pin for the facing system. GRS consists of alternating layers of compacted fill and closely spaced geosynthetic reinforcement. IBS is three main components: the Reinforced Soil Foundation, the GRS Abutment, and the Integrated Approach. This robust system blends the roadway into the superstructure for a jointless interface. For the reinforced abutments, engineers specified pinned segmental retaining wall units for their durability, ease of installation, and centering system that would help keep the courses running straight. This was the first time GRS-IBS technology was used in Vermont, and a first for installer Cold River Bridges LLC. The team created a footing of compacted 3/4-inch concrete aggregate and then placed the first layer of Diamond Pro PS 8 x 18 x 12-inch blocks in Granite Gray. The Diamond Pro PS system utilizes pins as a location device in installation. The pins are inserted in holes in the blocks before placing the backfill. When attaching the next block course, the cores are placed above the centering pins. This limits the movement of that upper course. After each course of block is laid, it is followed by stone then geosynthetic fabric, and then the block, stone, and fabric pattern repeat itself. In total, over 10,000 blocks were placed without the use of specialized equipment.
For the Hartland bridge, the entire existing structure was replaced with two single-span bridges using the GRS-IBS structures for abutments. Each bridge spans one barrel of the interstate eliminating 190 linear feet of bridge requiring future maintenance.
Using the GRS-IBS system, despite COVID delays, the work was completed in one construction season of six months from May to November. During that time, the bridge was closed, and traffic was detoured off Town Highway 41 through a privately owned gravel pit
Replacing the bridge’s superstructure would have required two years of construction and extended the life of the bridge by only 40 years. In contrast, by using GRS-IBS to replace the entire bridge, construction time took only six months and extended the life of the bridge to 100 years. The new, wider bridge was finished in one phase, before the winter season began, causing less disruption to local traffic. And perhaps best of all, using GRS-IBS technology cost $3 million less than replacing the superstructure of the previously existing bridge.